FIT AG vil globalisere additiv produksjon
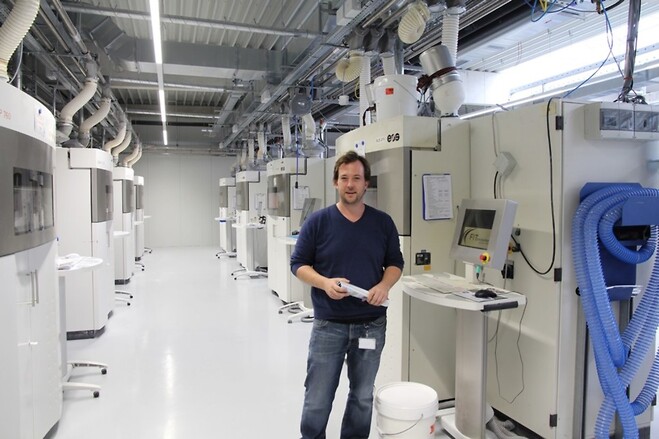
FIT Technology Group har spesialisert seg på innovative løsninger innen additive produksjon (additive manufacturing). Spekteret spenner fra å hjelpe kunder med design og lage prototyper til serieproduksjon. I tillegg utvikler FIT programvare og maskinvare. Alt under samme tak. I fjor solgte selskapet sin egenutviklete programvare netfabb til Autodesk. Siden har Autodesk gått inn som ti prosent eier av FIT AG.
Enorm vekst
Maskinregisteret møter Alexander Bonke, administrerende direktør for FIT Production GmbH, i de nye fabrikklokalene, et steinkast fra det gamle hovedkvarteret i Lupburg, like utenfor Nürnberg.
Direktøren er en relativt ung, men erfaren fagmann innen additiv produksjon, som forteller om hvordan FIT AG har bygget seg opp fra et enkeltmannsforetak i garasjen til grunnlegger og hovedeier Carl Fruth til et offensivt konsern. Fruth jobbet for den tyske maskinprodusenten EOS, men bestemte seg for å starte for seg selv for 21 år siden. Allerede i 2003 startet FIT med metallprinting og året etter lanserte man sitt egenutviklete ERP-system for fremstilling av prototyper. I 2005 investerte bedriften i sin første elektronsmeltemaskin og året etter lanserte man programvare for mikrostrukturer. Siden har det gått slag i slag med sertifiseringer innen fly- og bilindustrien samt FDA-godkjenning. I 2013 investerte FIT i sin første SLM Solutions 500 lasersmeltemaskin, året etter var det syv av dem i produksjon.
I dag har selskapet over 200 ansatte og virksomheten utvides nærmest kontinuerlig. Veksten og omsetningen øker i takt med utviklingen i selskapet og mens byggingen av den nye fabrikken er i gang planlegges det flere steg fremover.
Vil ta verden med AM
- Vi bygger en helt ny fabrikk som skal inneholde cirka 30 metallprintere og et titalls avanserte polymerprintere. Selv om vi er midt i byggefasen er vi allerede i gang med å produsere både i metall og polymer, forteller Bonke.
Han viser vei opp i andre etasje.
- Heldigvis besluttet vi å ha polymeravdelingen i andre etasje, for vi hadde faktisk ikke tenkt på hvor tungt metallpulveret er, så vi hadde litt flaks da vi valgte metall i første etasje, Bonke viser polymerprintere på rekke og rad, EOS er gjennomgående maskinvalg i denne avdelingen, men det finnes noen unntak.
- Se her, nå har vi som første kunde av Stratasys fått fargeprinteren J750 på plass, se så kult det er, sier Bonke mens han løfter på maskinlokket.
- Maskinen printer i alle farger, dette er jo et løft innen polymerprinting, kommenterer bedriftslederen.
Metall «for alle penga»
I første etasje står det for det meste SLM Solutions 500 maskiner med en, to eller fire laserkilder. Tre gamle EOS-maskiner står også og produserer.
- Vi satser på SLM Solutions fordi de lager «åpne» maskiner. Det vil si at vi kan selv konfigurere maskinene og derved ha full kontroll på alt vi gjør. Det gjelder i også de fire Arcam elektronstrålesmeltemaskinene, men det er en mye mer kompleks prosess da den er varm. Mens vi har noen titalls parameter å justere i lasermaskinene (SLM Solutions) har vi flere hundre i elektronstrålesmeltemaskinene. Vi trenger begge typer maskiner for å dekke ulike behov til kvalitet og komponentstyrke, forklarer Bonke.
Han peker på de stedene det blir enda flere SLM Solutions 500 maskiner.
- Allerede i dag er vi verdens største underleverandør av additiv produksjon i metall. Når året er omme har vi minst 14 SLM Solutions 500 maskiner, så du kan godt si at her er det «metall for alle penga», humrer den unge bedriftslederen.
Skal «ta verden med AM»
Fabrikken vi rusler rundt i er som sagt under oppføring og denne er starten på et globalt eventyr som FIT AG planlegger.
- Vi bygger først denne fabrikken ferdig. Så optimaliserer vi alle prosesser slik at vi skaper en industriell standard som senere blir malen for våre fremtidige fabrikker. Disse vil vi bygge i USA, Japan og andre steder etter som markedene modnes, sier Bonke.
Hvor fort vil denne prosessen gå?
- Vel, vi jobber på spreng med å bli ferdig, ikke bare med ny fabrikk, men også nytt hovedkontor ved siden av fabrikken, så får det gå seg til før vi ruller ut konseptet vårt. Vi er godt i gang med automatisk pulvertransport og andre automatiske systemer, men vi jobber også med prosesser, eksempelvis produktdesign for å kunne fjerne støttematerialer automatisk. Vi ligger langt fremme innen additiv produksjon (additive manufacturing), men vi skal bli enda bedre før vi går videre, svarer Alexander Bonke.
Rask utvikling, men…
Til tross for bransjens enorme vekst er det en del skjær i sjøen.
- Kundene er den største utfordringen. De kan lite eller ingen ting om additiv produksjon og kommer med alskens underlige forespørsler. Det klassiske eksempelet er at kunden gjerne vil ha laget et eksisterende produkt med additiv produksjon. Det går bare ikke. Det er ytterst viktig å forstå at skal man lykkes med additive prosesser må produktene konstrueres og formgis for additiv produksjon! Alt annet blir rett og slett ikke lønnsomt, understreker Bonke.
Han forteller at det er mye konservatisme som bremser utviklingen.
- De som er mest på hugget er racerbilprodusenter. Der skal alt gå så fort som mulig så de er veldig motiverte til å ta i bruk additiv produksjon. Medisinsk sektor er også offensive, mens tradisjonell industri og verktøymakere sitter litt på gjerdet.
Må læres opp
Et av tiltakene som vil hjelpe er opplæring.
- Vi kjører kundene våre på solid opplæring og er i gang med å utvide tilbudet ved vårt avdelingskontor i Hamburg. Her forsøker vi å påvirke kundene til å tenke nytt, bruke all erfaringen de har fra før sammen med den nye kunnskapen rundt additive prosesser. Det handler om bevisstgjøring og å løfte kunnskapsnivået flere hakk. Det blir mye å lære mens man går, men når du kan drastisk redusere vekt og antall komponenter kan du også skape store verdier. Et eksempel fra vår virksomhet er at vi reduserte en enhet til racerbil fra 187 komposittkomponenter til en eneste titanprintet komponent. Resultatet var helt fantastisk på alle måter, men du får ikke vite mer, sier Bonke hemmelighetsfullt mens han viser frem bilder og en testvideo av bildelen.
Kvaliteten økes
FIT henter verdifull erfaring fra racerbilprodusenter, men også fra sine andre kundesegmenter.
- Det er veldig høye krav både innen fly, bil og medisinsk sektor. Siden dette er våre hovedmarkeder får vi de samme strenge krav til kvalitet som alle andre som leverer til disse industriene. Det er en fordel, for da må vi skjerpe oss for å holde oss i front, understreker Bonke.
Han forteller videre at FIT AG nå investerer i en CT-skanner.
- CT-skanner vil gi kundene en verdifull dokumentasjon på at deres komponenter ikke inneholder sprekker eller andre feil. Hos oss har vi full sporbarhet og dokumentasjon i alle ledd av produksjonen, fra råvare til ferdig testet komponent. Dette vil kanskje også åpne dørene for nye markeder, eksempelvis offshore og subsea.
Kostreduksjoner på gang
Noe av utfordringen er at additiv produksjon ofte er forbundet med høye kostnader. Dette skyldes både pris på maskiner, metallpulver og andre investeringer som må til for å oppnå industrikvalitet på de metallprintede produktene.
- De neste årene vil vi se en stor kostnadsreduksjon. FIT er i full gang med å optimalisere hele verdikjeden og vi forventer å redusere prisen per produsert metallgram til en sjettedel innen 2020. Det blir store besparelser også innen polymer. Markedet kommer til å vokse radikalt de to til tre neste årene og da følger priser på teknologi og råvarer med. Slik vi ser additiv produksjon i dag må du ha ti maskiner for å ha inntjening. Med 20 maskiner kan du tjene gode penger. Vi regner med å ha rundt 30 metallprintere innen utgangen av året og det blir det god butikk av.
Ta kontakt!
I Norge har vi i dag totalt kun fire metallprintere. Vi mangler kompetanse innen en rekke områder, og det er mange bedrifter som nøler med å gå i gang med additiv produksjon. Hvilke råd vil du gi dem?
- For det første vil jeg helle litt kaldt vann nedover ryggen; innen additiv produksjon finnes det ikke noe «quick fix». Ting tar tid. Som sagt er det mange kunder som kommer til oss med et feil sett av forventninger. Ta tid til opplæring i egen bedrift, det er første prioritet. Send folk på kurs, søk kunnskap hos dem som har vært med en stund. Kom på banen med komponenter konstruert for additiv produksjon. Gjør du ikke det kan du glemme suksess med denne teknologien. Beregn god tid før planlagt produksjonsstart. I snitt ser vi at det fort går et par år fra ide til produsert komponent. Årsaken til det er delvis at det kreves mer verifisering og dokumentasjon på kvalitet enn det som gjelder for andre produksjonsformer. Dette skyldes flere forhold, blant annet mangel på historiske data, simuleringer, tester og ikke minst at flere bransjer ennå ikke har kommet med sine dokumentasjon- og prosesskrav til additiv produksjon. Det er viktig å komme i gang, så nøl ikke! Er det noen som lurer på noe så er det bare å kontakte oss, svarer Alexander Bonke.
For mer informasjon besøk: www.pro-fit.de eller www.fit-prototyping.de