Additiv produksjon konkurrerer ut støpegods
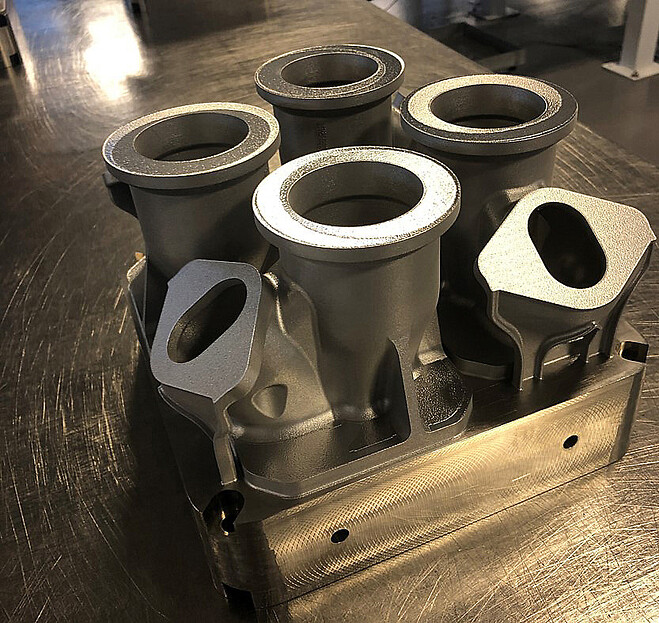
Ingeniørene hos GE Aviation og GE Additive har byttet fire eksisterende deler fra støpegods til 3D-printing i metall - og ser potensialet for hundrevis til. Kostnadene ved additiv produksjon kan konkurrere med støping.
De fleste produsenter ville aldri drømme om å bytte fra en presisjonsstøpt del til en produsert med additiv produksjon (AM), spesielt hvis de allerede hadde betalt for støpeformen. Likevel er det akkurat det GE Aviation gjør med fire luftingsdeler fra en land/marin turbin. De tok avgjørelsen basert på pris og tid til markedet.
Billigere og raskere med AM
Et samarbeid mellom GE Aviation og GE Additive viser at additiv produksjon i metall kan gå side om side med konvensjonelle støpegods på pris. Faktisk forventer ingeniørteamet at dets fire 3D-produserte deler vil kutte opp til 35 prosent av kostnadene. Det er nok til å rettferdiggjøre å trekke tilbake de gamle støpeformene for alltid.
Like viktig tok konverteringsprosessen bare ti måneder å gå fra å identifisere måldeler til endelige prototyper for 3D-printing. Vanligvis tar det 12 til 18 måneder eller mer å produsere deler til luftfart og land/ marine turbiner ved hjelp av en støpeprosess.
- Dette forandrer spillereglene, sa GE Aviation’s produksjonsleder for tilsetningsstoffer Eric Gatlin.
- Dette er første gang vi har gjort en del-for-del-utskifting, og det var billigere å gjøre det med additiv fremstilling enn med støping. For å sikre at vi demonstrerte kostnadskonkurranseevne, hadde vi fire eksterne leverandører som prissatte delene, og vi kom fortsatt lavere med additiv produksjon. Dette er bare begynnelsen. Prosjektet har identifisert mange andre deler på en rekke motorer som de kan konvertere til additiv og spare kostnader, understreker Gatlin.
Presser frem endring
Den additive industrien har vokst seg mer konkurransedyktig i mange år. Dette gjelder spesielt for nye flymotorprogrammer. Den 3D-printede drivstoffdysespissen til GE Aviation’s LEAP-motor konsoliderer for eksempel 20 forskjellige deler - og trinnene som trengs for å bearbeide og montere dem - i en enkelt struktur. Selskapets nye turbopropmotor tok det til et annet nivå ved å kombinere forbløffende 855 deler til bare 10 3D-fremstilte komponenter. I begge tilfeller (og andre) benyttet GE Aviation seg av delekonsolidering for å presse store kostnadsbesparelser ved å montere disse delene.
Etter hvert som antallet krevende applikasjoner økte, prøver produsenter å forbedre produktiviteten til metallaserprintere, som bygger deler av metallpulver, ett tynt lag om gangen.
Et eksempel er GE Additives Concept Laser M2 Series 5-maskin. Dens to lasere smelter og sammensmelter metallag raskere enn en enkelt laser alene, og gir mer konsistente resultater for komplekse konstruksjoner. M2s lasere er også kraftige, enten 400 watt eller 1 kilowatt, og produserer 50 mikron tykke lag. Den har også et stort byggekammer på 21.000 kubikkcentimeter å lage deler i. Forbedring av produktiviteten senker kostnadene, og det reduserer også utviklingstiden.
- Vi sa rett og slett at vi skulle velge et materiale vi allerede hadde kvalifisert, sier Gatlin, og fortsetter:
- I produksjonen valgte vi M2 fordi vi kjenner den godt. Og vi hadde ikke tenkt å gjøre noen store designendringer, bare noen justeringer slik at vi kunne printe ut delene med hell. Vi forenklet så mange trinn vi kunne, så teamet kunne jobbe fort.
Dette gjorde det mulig for prosjektgruppen å utvikle endelige prototyper mellom april og september 2020. Selv om alle fire delene ble beregnet for LM9000, en land/marine turbin avledet fra GE90 turbojet, som GE Aviation bygger for Baker Hughes, vurderte gruppen dusinvis av deler til eldre motorer og produkter også.
- Luftfartbedrifter leverer reservedeler for hele produktets levetid, forklarer Joseph Moore, senior prosjektleder og prosjektleder fra GE Aviation.
- Hva skjer, spør han, når det bare er en håndfull reservedeler igjen og en leverandør planlegger å avvikle materialet de er laget av? Vi må finne ut hvordan vi kan komme med utskiftninger før vi går tom for deler, sier Moore, og legger til:
- Vi må gå raskt gjennom utviklingssyklusen og lage en del vi faktisk kan sende til kunden. For å bevise at vi kunne gjøre det, ble vi satt under en frist og fikk beskjed om å gjøre delen så raskt og kostnadseffektivt som mulig. Målet vårt var alltid å se på måter å endre produksjonen på. Det er bare noen få leverandører som lager investeringer for luftfartsindustrien, så vi må ha muligheter for å sikre at vi ikke blir påvirket av foreldelse og er avhengige av kostnadsmodellene til spesifikke leverandører. Hvis vi kan lage en additiv del for mindre, kan vi spare penger nå og unngå prisøkning i fremtiden, understreker Moore.
Årlig revisjon
Veien til å velge disse fire delene startet tidlig i 2020 med GE Aviation’s årlige revisjon av støpegods.
- Vi ønsker alltid å trekke ut kostnader fra eksisterende produkter, så spør vi: Blir vi mer konkurransedyktige? Er det ting vi ikke kunne gjøre for et år siden som nå er teknisk gjennomførbare, sier Gatlin.
Testprosessen vurderte både nye og eldre produkter. Det ble vurdert en rekke faktorer, for eksempel funksjonene til GE Aviations 3D-printere, delstørrelse, form og funksjoner. Ingeniørene spurte om delene brukte godt karakteriserte materialer de hadde jobbet med på maskinene før. De tok også hensyn til de enkelte trinn i etterbearbeiding, som eksempelvis maskinering for å eliminere overflatefeil og lodding for å legge til beslag til en del.
Additiv produksjon er perfekt for å lage komplekse deler, for eksempel de med interne kanaler. Additivt fungerer også bra for deler med enkle geometrier, siden de er relativt raske og enkle å printe ut fra eksisterende modeller, og de eliminerer tid og investering i form eller verktøy som er nødvendig for støping. Man så på både reservedeler med lite volum og deler til produksjonsvolum for nye programmer, som LM9000-motoren.
I februar 2020 hadde GE Aviation-teamet allerede identifisert 180 støpte deler som de trodde 3D-print potensielt kunne spare penger. For å være sikker delte et team ingeniører hos GE Aviation og et hos GE Additive, hver som bruker sin egen organisasjons produksjons- og økonomiske modeller, i små grupper for å beregne avkastningen på utskrift av hver del. Så feide Covid-19 over kloden.
Produksjon i pandemien
Viruset økte produksjonen over hele verden. På GE Aviation sitt produksjonsanlegg for additiv produksjon i Auburn, AL, USA, hvor deler til andre GE Aviation-motorer er laget, ga pandemien en mulighet for teamet til å fokusere på andre prosjekter. Uventet hadde de maskin- og etterbearbeidingstid tilgjengelig for å begynne å lage deler. Prosjektet ble født for å dra nytte av disse maskinene.
- Vi er en produksjonsbutikk og vil ikke se et prosjekt som dette før etter at GE Aviation’s Additive Technology Center hadde utviklet prosessen for lavprisproduksjon, uttaler Jeff Eschenbach, senior prosjektleder og prosjektleder ved Auburn-anlegget.
- Det som var annerledes med dette prosjektet er at vi startet dette helt fra begynnelsen. Det skapte en mulighet for ingeniørene her på stedet for å bli involvert.
Lagets dannelse sparket alt i høyt gir. Dusinvis av deler hadde bestått den første sekelsjonsprosessen. Ytterligere analyser resulterte i at det ble valgt ni deler fra dem. De inkluderte deler på andre marine-industrielle gassturbinemotorer, turbojet og noen militære programmer. Delene var alle laget av enten CoCr, en legering av kobolt og krom som er mye brukt til varme-turbindeler, eller Ti-64, en stiv, lett titan-aluminium-vanadiumlegering som brukes til strukturelle deler. De så bare på deler som kunne passe inn i Concept Laser M2-maskinen.
Teamet begrenset det videre, og prioriterte deler basert på tekniske ressurser og viktigheten av kostnadsbesparelser for motorprogrammet. Teamet slo seg ned på fire deler - adapterhetter til LM9000s luftsystem - som ble fokus for programmet på Auburn.
Alle fire var omtrent 3,5 tommer i diameter og omtrent seks tommer høye. De skulle lages av CoCr for å håndtere den varme trykkluften fra turbinens kompressorseksjon.
Fra et produksjonsperspektiv delte de en basisgeometri og lignende funksjoner. Teamet antok at M2 kunne skrive ut tre deler om gangen, men ingeniører redesignet snart byggeplateoppsettet for å øke det til fire. Dette økte produktiviteten umiddelbart, fordi det tar omtrent like lang tid å skrive ut fire deler som tre deler.
- Ved hjelp av simulering og analyse viste teamet at delene utførte det samme som de støpte delene de byttet ut, sier Steve Slusher, en produksjonsingeniør for GE Additive på prosjektet.
Teamet bygde også teststenger med hver printing, noen i det åpne hulrommet på hetten som gikk ned til byggeplaten, slik at teknikere kunne måle integriteten til hvert produksjonsløp.
Læring
Prosjektet var en stor suksess. Det markerte første gang GE Aviation hadde skiftet produksjon fra presisjonsstøping til additiv produksjon basert på kostnad.
- Delene var en-til-en-erstatning, uten redesign eller konsolidering av deler for å forbedre økonomien. Og det ble gjort raskt, forteller Gatlin.
- Det som imponerer meg er at vi kan ta et eksisterende støpedesign, replikere det raskt på printerene våre, og i løpet av noen uker etter at vi startet prosjektet, var de siste delene av samme kvalitet som deres støpte kolleger. Dette prosjektet fungerer som en mal for fremtidig arbeid, uttaler Eschenbach.
Kelly Brown, senior teknisk leder i GE Additive, er enig:
- Fra et forretningsmessig perspektiv viste Auburn muskler vi ikke hadde tidligere, og nå har vi en gruppe deler som vi kan gå i gang med. Det teamet har gjort er bemerkelsesverdig, og det viser virkelig deres evner.
Å bytte investeringsdeler til 3D-utskrift i metall er noe de fleste produsenter aldri vil drømme om å gjøre. Men ingeniører fra GE Aviation og GE Additive gjorde det, og deres nye virkelighet lover å spare dem tid og penger for dusinvis og til slutt hundrevis og tusenvis av deler gjennom alle produktlinjene.
For mer informasjon se: www.ge.com/additive
Kilde: GE Additive