Ny dreiesort ga store besparelser
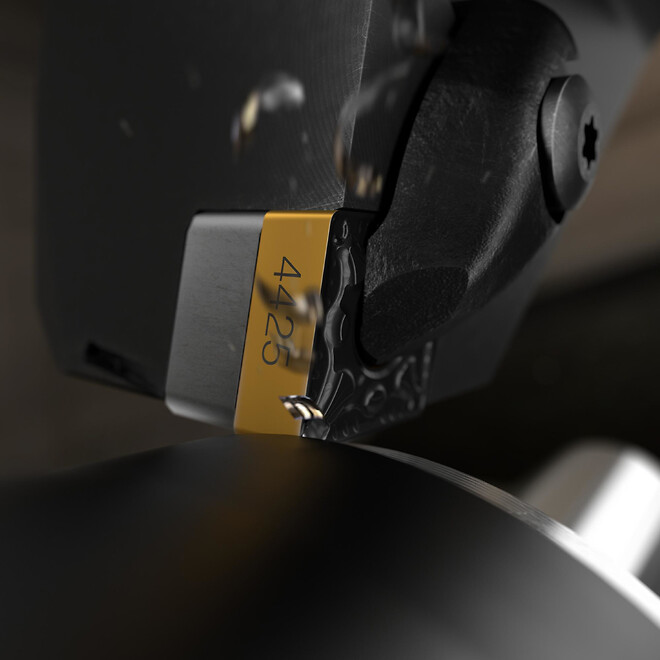
Sandvik Coromant forteller hvordan deres nye ståldreieskjær hjelper THK Rhythm med å ta kontroll over maskineringsprosessen.
Tillsonburg er en del av en blomstrende kanadisk bilregion, og hjemmet til bilfabrikken THK Rhythm som betjener globale produsenter inkludert BMW, Ford og Daimler Mercedes Benz. Et tøft, konkurransedyktig landskap gjorde at THK Rhythm trengte å få tilbudet sitt til å skille seg fra konkurrentene. For å gi produktene sine fordelen, fikk selskapet støtte fra Sandvik Coromant og de nye dreiekvalitetene for stål.
Fokuserer på OEE
THK Rhythm bilfabrikken spesialiserer seg på fjæringskomponenter som finnes i kjøretøy over hele verden, sammen med kuleledd og kulebolter for disse komponentene. Å være en global bilaktør krever strenge kvalitets- og kostnadsoptimaliseringstiltak, noe som er tydelig i THK-anlegget.
THKs kvalitetspolicy, som vises tydelig ved anleggets inngang, lyder: rett første gang, rett hver gang, forbedres kontinuerlig. Og det er mer enn bare et fengende mantra. Flere produksjonsforbedringer viser denne politikken, inkludert Kaizen, japansk for kontinuerlig forbedring, som fokuserer på å optimalisere effektivitet, produktivitet og generell utstyrseffektivitet (OEE).
Utfordrende maskineringsprosess
Til tross for THKs krystallklare effektivitetsmål, var det en utfordring å nå produktivitetsmål og kontrollere kostnadene ved produksjon av den fremre nedre strekkarmen, en komponent som går inn i fjæringsenheten til en bil.
- Den fremre nedre strekkarmen krever fjerning av mye materiale under flere trinn, inkludert boring, grovbearbeiding og etterbehandling av en boring, forklarer Adrian Dabrowski, prosessingeniør ved THK Rhythm.
Komponenten er laget av et smidd ISO P-stål som er spesielt slipende, med høy strekkfasthet. Maskinering av denne delen krever et spesialverktøy med et antall skjær som er forskjøvet eller trinnvis - noe som betyr at de ikke alle har samme diameter. Den opprinnelige bearbeidingsprosessen for den nedre fremre strekkarmen ble designet for å lage 140 deler per verktøy, men THK kunne bare produsere omtrent 92 stykker i gjennomsnitt før et av skjærene på den største diameteren sviktet, noe som førte til at hele verktøyet sviktet.
Mye nedetid
Hyppige feil førte til at operatører måtte bytte verktøy altfor ofte. Maskinene i THK Rhythm-verkstedet er satt opp slik at dersom ett verktøy går i stykker, hentes det automatisk inn et reserveverktøy slik at maskinene kan fortsette å gå. Med hyppige verktøyfeil var det imidlertid ikke nok reserveverktøy til å holde produksjonen flytende.
Sponkontroll, en viktig faktor for enhver ståldreioperasjon, var også en bekymring.
- Når verktøyet sviktet, ble spon ofte pakket rundt det; så vi måtte fysisk ta ut verktøyet og fjerne sponene. Disse sponene var skarpe og kunne forårsake kutt i fingeren og skader, avslører Gary Martin, maskinoperatør ved THK.
Dabrowski fremhever videre ulempene ved verktøysvikt:
- Vi kjørte maskinene med bare ett enkelt verktøy, og da verktøyet gikk i stykker, måtte operatørene fysisk ta det ut, manuelt bytte alle skjærene og sette det tilbake i maskinen. Det tilsvarer rundt fem til seks minutter med nedetid per maskin, som raskt summerer seg. I gjennomsnitt betjener operatører tre maskiner. Så hvis én maskin er nede, er i hovedsak alle tre nede. På gode dager hadde vi bare ett brudd per skift. På disse dagene var nedetidene så hyppige som tre til fire ganger per skift per maskin, fortsetter Dabrowski.
Ved å bruke de tidligere skjærene var det mye nedetid, noe som gjorde det vanskelig å nå daglige produktivitetsmål.
Jakten på en løsning
I jakten på den rette løsningen prøvde THK å justere maskinene på daglig basis, finjustere matehastigheter og omdreininger per minutt (o/min). Teamet prøvde også ut ulike skjær og geometrier fra et par verktøyleverandører, men ingenting traff blink. Det var helt til THK henvendte seg til Sandvik Coromant.
Sandvik Coromant la til to høyytende hardmetallskjærkvaliteter, GC4415 og GC4425, til sitt eksisterende utvalg på slutten av 2020. Skjærene har et bredt spekter av bruksområder og anbefales for både kontinuerlige og avbrutte kutt. Mens GC4425 gir forbedret slitestyrke, varmebestandighet og seighet, komplementerer GC4415 GC4425 der forbedret ytelse og bedre varmebestandighet er nødvendig. For THK Rhythm var GC4415 et passende tillegg til maskineringsprosessen.
Begge kvalitetene inneholder andre generasjons Inveio-beleggteknologi.
- Det som gjør dette verktøybelegget spesielt unikt, er at det kan undersøkes på mikroskopisk nivå, forklarer Rolf Olofsson, produktsjef i Sandvik Coromant.
Materialets overflate har en ensrettet krystallorientering. Hver krystall retter seg opp mot skjærekanten, og skaper en sterk barriere som forbedrer krater- og flankeslitasjemotstand. Varme ledes også raskere bort fra skjæresonen, noe som holder skjærekanten i form for lengre tid i skjæringen.
- GC4415 og GC4425 kan maskinere et større antall deler, samtidig som de bidrar til forlenget verktøylevetid, eliminerer plutselige brudd og reduserer omarbeiding og skrot. For THK er GC4415-innsatsen løsningen på svingproblemene, fortsetter Olofsson.
Kjører fremover
Siden introduksjonen av GC4415 til maskineringsoperasjonene, har THK sett produktiviteten på fabrikkgulvet endre seg til det bedre. Faktisk, fordi de kjører med høyere skjærehastigheter, opplevde THK en produktivitetsøkning på 11 prosent så snart operatørene begynte å bruke skjæret.
I løpet av de fire første månedene av 2021 brukte THK omtrent 3800 skjær av deres tidligere foretrukne sort. Da GC4415-kvaliteten ble introdusert i mai 2021, brukte verkstedet bare 3000 av de nye innsatsene i samme tidsramme – en reduksjon på 18 prosent i antall innsatser som ble brukt, noe som dramatisk forbedret den totale kostnaden per del.
Endring handler ikke bare om tall
- På fabrikkgulvet er våre operatører mer fornøyde ettersom de kan fokusere på å laste deler og ikke å måtte bekymre seg for hyppige verktøyskift eller sponstopp. Den nye sorten har bidratt til å spare 194 timer produksjonstid per år. Takket være GC4415 opplever THK Rhythm-verkstedet nå langt mindre nedetid og mer pålitelig produksjon, konkluderer Dabrowski.
Etter suksessen til GC4415-skjærkvaliteten i maskinering av kjøretøyets fremre nedre strekkarmer, planlegger THK Rhythm nå å teste og introdusere kvaliteten i andre deler av produksjonslinjen, for eksempel kulebolter og kuleledd.
For mer informasjon se: www.sandvik.coromant.com og www.thk-rhythm-auto.eu
Kilde: Sandvik Coromant