Klinger Westad - fremtidsrettet 125-åring med mer automasjon
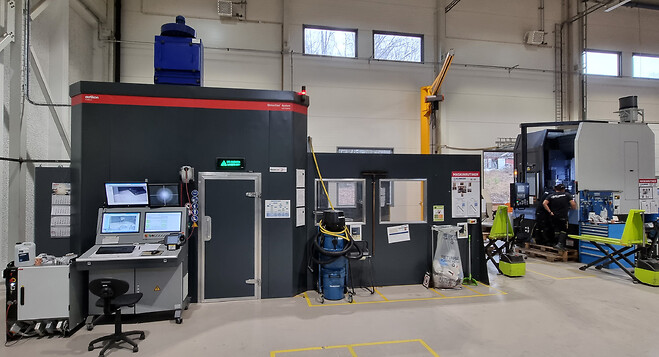
I 2020 var det 125 år siden Westad Armaturfabrikk ble startet av Sandefjordmannen Daniel Westad. Bedriftshistorien er interessant og spennende og etter at det østerrikske selskapet Klinger tok over eierskapet har det skjedd mye positivt på Geithus.
Klinger Westad AS holder til på Geithus cirka 35 km nord-vest for Drammen. Ved oppstarten i 1895 produserte selskapet ventiler til lokal tremasse- og papirindustri. Ulike overganger i bransjen gjorde at Westad begynte å betjene den marine industrien rundt 1950.
Med ankomsten av olje- og gassproduksjon til Norge på slutten av 1970-tallet, tilpasset Westad sine produktlinjer for å betjene dette krevende markedssegmentet. Materialkravene økte, og Westad leverte til sitt rykte. Spesialmaterialer i rustfritt stål som titan, Duplex, Super-duplex og 6MO ble de vanlige materialene for ventiler i krevende miljøer.
Ledende leverandør
I dag designer og produserer Klinger Westad dobbelt- og trippeloffset-spjeldventiler med høy ytelse i foretrukne materialer for LNG, LPG, kjemikalier og andre kritiske bruksområder.
Spesifikke bruksområder i den marine industrien inkluderer; LNG-tankere,
LPG og LEG tankskip systemer, kjemikalie- og produkttankere.
Landbaserte og offshoreapplikasjoner er; LNG flytende, håndtering og lagringsfasiliteter, kritiske sjøvannsystemer på olje- og gassproduserende plattformer samt service innenfor etsende i gruveinstallasjoner.
Fremtidsrettet 125-åring
Selv om markedskonjunkturer har påvirket virksomheten har selskapet levert solide tall gjennom en årrekke. Erik Tøien, prosjektleder hos Klinger Westad, tar oss med på en omvisning gjennom hele fabrikken.
- Mye av grunnen til at bedriften gjør det bra over tid er at vi har en god bedriftskultur og svært dyktige folk. Vi utvikler og produserer kvalitetsprodukter og løsninger som verdsettes av kunder over hele verden. Samtidig viser en fremtidsrettet ledelse tydelig investeringsvilje til å drive frem både nye produkter og modernisere produksjonsteknologien her på huset, noe du nå skal få se, sier Erik Tøien.
Kan kjøre ubemannet døgnet rundt
Tøien viser frem en del av produktene som skal bli til ventiler om bord i ulike typer gasstankskip. Støpegods ligger klare til maskinering på lager og ute ved CNC-maskinene.
- Som du ser har vi mange ulike produkter som ferdigmaskineres i forskjellige maskiner, noen er enkeltstående maskiner mens andre er i egne celler. Erik stopper opp og viser frem en automatisert celle. Han gestikulerer og peker mens han forteller:
- Vi installerte en Mazak HCN 6800 horisontalt maskineringssenter i 2015. Den har verktøymagasin for 160 verktøy og palettstørrelse på 630x630 mm. Det er Mazaks egne FMS Palletech 12 paletter i to etasjer. I 2019 kom den andre maskinen i cellen, en Mazak Integrex i630 Vertikal flerfunksjonsmaskin. Også den med 160 verktøyplasser. Nå utvidet med Palletech til 32 paletter og en ladestasjon til. Begge maskinene har high torque spindel og utstyrt med overvåking for ubemannet kjøring, så når vi har svært mye å gjøre kan vi kjøre ubemannet døgnet rundt.
Har dere ofte så mye å gjøre?
- Ikke nå for tiden, men vi får topper der denne cellen virkelig gjør nytte for seg, vel verd investeringen, svarer prosjektlederen.
Kan tilby lasersveising
Hos Klinger Westad benyttes helautomatisk fiberlasersveiseteknologi for sin ventilproduksjon. Lasersveisecellen har en 6-akse ABB-robot som gjør det mulig å behandle selv de mest komplekse overflatestrukturer. Laserkilden er på 6 kW. Teknologien gjør at Klinger Westad kan produsere svært spesifikke ventiler for marin industri.
Akkurat som det finnes ventiler for omtrent alle bruksområder i prosessindustrien, har individuelle industrier også svært spesifikke ventiltyper og egenskaper. I denne sammenheng er den maritime industrien intet unntak: Skivene til for eksempel LNG-ventiler må belegges med et ekstra lag – typisk Stellite, et koboltbasert materiale – for å sikre at tetningsoverflaten ikke kan ripes eller utvikle andre defekter.
Tidligere har man outsourcet denne delen av produksjonsprosessen, også kjent som "hard facing", til en underleverandør i Norge.
- Det er vesentlig mer kostnadseffektivt å utføre denne prosessen i eget hus, sier Tøien.
Har dere fullt belegg i lasersveisecellen?
- For tiden ikke, så vi kan tilby denne tjenesten til eksterne kunder, svarer Tøien.
Fremoverlent 125-åring
Ferden går videre til lakkavdelingen.
- Vi foretar all overflatebehandling her på huset og som du ser har vi et stort våtlakkanlegg. Her har vi i prinsippet kapasitet til å betjene eksterne kunder, forteller Tøien, mens vi vandrer videre, gjennom monteringsavdelingen til avdelingen for trykktesting.
- Vi har investert i nytt trykktestsenter, i eget spesialbygget rom. Her gjennomgår ferdige ventiler omfattende testing før de godkjennes for levering til kunde. Alle våre produkter er sporbare, helt fra råvare til ferdig dokumentert godkjent test. Du kan gjerne kalle oss en industri 4.0-bedrift, for det er det vi er i praksis. Også i trykktestavdelingen har vi kapasitet til å teste for eksterne kunder.
Erik Tøien er ikke ferdig med omvisningen. Vi går bort til en helt ny robotisert produksjonscelle. Her skal ventilringer maskineres, vaskes og merkes før de plasseres i et automatlager. Artikkelen om denne cellen kan du lese om et annet sted i dette bladet.
- Som du ser, vi får da til noe her på Geithus, 125 års erfaring gir god ballast, konkluderer Erik Tøien.
For mer informasjon se: www.klinger-westad.com