Sveiser utendørs - satser på Fronius
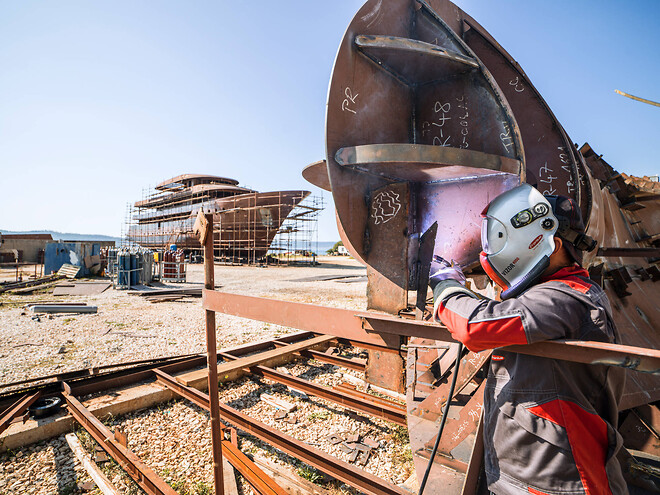
Sol, salt og tungt stål, sveising og mange andre utfordringer innen skipsbygging løses på skipsverftet Gulet i Kroatia. Med Fronius sveiseteknologi får sveiserne en enklere arbeidsdag.
Sveising innen skipsbygging er definitivt en tøff oppgave. Det kroatiske verftet Gulet j.d.o.o vet hvordan de skal rapportere: trange rom krever høy dyktighet og riktig valg av sveiseposisjon. Liggende sveising eller sveising på knærne er en del av hverdagen. På dagsordenen til Gulet står det kun konstruksjon av cruiseskip. Helt fra starten av har verftet stolt på sveiseteknologi fra Fronius: høy kvalitet, lav vekt og ekstremt enkel håndtering var overbevisende faktorer.
Sveiser alt utendørs
Den bratte og steinete kysten til det kroatiske Adriaterhavet med en bakgrunn av turkisblått vann strekker seg over 6000 kilometer og er et paradis for båtentusiaster. I tillegg til all vannsport, blir det å ta et cruise gjennom denne idylliske øyverdenen stadig mer populært. Foreløpig er det mest store yachter som blir brukt. De mange historiske kystbyene er også blant reisemålene – inkludert Trogir, som imponerer med sin fortryllende gamleby. Samtidig er det også hjemmet og havnen til Gulet-verftet. Etter etableringen i 2015 har fabrikken, som i dag har 16 ansatte, allerede produsert åtte skip:
- Du må planlegge rundt et halvt år for et skip. Men siden vi utfører alt sveisearbeid utendørs, avhenger den faktiske byggetiden sterkt av værforholdene, forklarer Mirko Purić, eier av Gulet.
Lite firma – store utfordringer
På verftet til Purić sveises det selvfølgelig også for hånd. Her brukes det for det meste stål, og det er derfor de fire trente og profesjonelle sveiserne hovedsakelig bruker MIG-prosessen. Å finne førsteklasses sveisere er imidlertid vanskelig, forklarer eieren av verftet, fordi de må mestre alle tre sveiseposisjonene for sveisetesten: vertikal-, horisontal- og vinkelsveising. Nettopp derfor satset Purić utelukkende på sveisesystemer fra Fronius helt fra begynnelsen av, ettersom systemene støtter de nødvendige ferdighetene på en omfattende måte.
- Jeg jobbet tidligere med forskjellige systemer fra konkurrenter, men ingen kunne nå opp til Fronius. Kvaliteten på systemene, den lange levetiden og de forhåndsinnstilte parametrene, som inkluderer riktig trådhastighet for hvert materiale og hver materialtykkelse, overbeviste meg. Smeltebadet flyter ut i sømmen som om det skulle vært støpt, sier Purić begeistret.
I tillegg har han ikke registrert noen feil, til tross for de vanskelige forholdene på stedet: Alle skip på Gulet bygges utendørs ved kaien, noe som gjør sjøsetting lettere på grunn av nærheten til vannet. Men siden det ikke er noen overbygde hallanlegg tilgjengelig, utsettes arbeidere og maskiner for været 365 dager i året: regn, fuktighet og høye temperaturer på opptil 50 grader om sommeren. Bare tre små containere fungerer som lagringsplass for maskiner og gassflasker, i tillegg til å fungere som kontorlokaler.
Arbeidet kan føre til at man blir veldig svett, ikke bare på grunn av den enorme varmen om sommeren, men også på grunn av den begrensede plassen inne i skipet. Rundt 50 prosent av et skip sveises liggende eller på knærne. Spesielt når du nærmer deg sidene på skipet, blir tilgjengelig plass – på grunn av skrogets form – mindre og mindre. Ved baugen, i den fremste delen av skipet, er det ikke uvanlig med flater på mindre enn 40 cm.
- Det gjør jobben veldig krevende, og det er derfor det er så vanskelig å finne førsteklasses sveisere, forklarer Purić.
Nøyaktige kontroller av stålplatene og sveisesømmene
Gulet bygger primært cruiseskip med en maksimal lengde på 120 meter. Til det meste av skipsstålet brukes det hovedsakelig rørtråder med en diameter på 1,2 mm. Pulverfyllingen danner slagg rundt sveisesømmen, noe som i stor grad reduserer sprutdannelse. Dette er av enorm betydning for senere godkjenninger, siden utseendet til en søm er avgjørende, i tillegg til robustheten. Verftet må også gjennomgå en rekke strenge kontroller. Alle metallplater som er montert i skipet, testes og må ha et Lloyd-stempel når de forlater fabrikken. Germanischer Lloyd (GL) er et internasjonalt testinstitutt.
- Jeg må ta med metallplater uten et Lloyd-testsertifikat til verftet i Split for en hardhets- og bøyetest. Dette er den eneste måten jeg kan være sikker på at stålplatene vi behandler, ikke har kvalitetsfeil, sier Purić.
Skipene på Gulet bygges i seksjoner. Når et element er satt sammen, kommer det en kontrollør fra ekspertorganet – totalt minst ti ganger i løpet av byggeprosessen. Når for eksempel kjølen, den viktigste lengdestrukturen av skipet, kobles til ytterkledningen, blir alt materiale sjekket av eksperten. Sveisesømmene på ytterkledningen er vanligvis belagt med kalk og innsiden med petroleum. Hvis petroleumet lekker til den andre siden, indikerer dette et hull i sveisesømmen. Sveisesømmen må derfor repareres ved at den freses ut, slipes av og sveises igjen.
I tillegg blir det tatt røntgen av rundt 30 prosent av støtfugene på et skip. Små sorte prikker på bildet indikerer at splinter fra slagget kan ha blitt sveiset med. Sømmen er dermed porøs og må uansett repareres. Hvis det er flere sveiselag, må slagget fjernes nøye, fra rotlaget og helt til mellom- og fyllingslagene.
- Kravene er strenge, men vi fokuserer på kvalitet for å overbevise kundene våre, understreker Purić.
Klientellet består for det meste av private selskaper som er aktive innen sjøfartsbransjen. Skipsbyggerens portefølje inkluderer også båter for havfiske – den første tråleren er allerede i produksjon. Ytterkledningene på disse skipene må ikke være mer enn 16 millimeter, fordi Gulet kun er sertifisert opp til denne tykkelsen. For alle tykkelser over dette må det søkes om ytterligere testsertifikater, som igjen er forbundet med høye kostnader.
Høy sveiseytelse og en pålitelig partner
- Maskinene er lette og derfor enkle å transportere på byggeplassen så vel som i skipet. TransPocket 1500 veier mindre enn fem kilo. Dette er grunnen til at vi først og fremst bruker den til heftearbeid der elektrodesveiseprosessen anvendes. For alt MIG-sveisearbeid bruker vi TransSteel 5000 som veier rundt 30 kg. Vi har totalt fire av denne på lageret, forteller Purić, og fortsetter:
- Enkel bruk av systemene er også et avgjørende pluss for sveiserne. Hvis en nyansatt starter å jobbe hos oss, mestrer han systemene etter en times instruksjon, sier Purić med overbevisning, og legger til:
- Hovedårsaken til at jeg valgte Fronius er imidlertid kvaliteten på sveisesystemene, fordi de fungerer uten problemer. Dette betyr at jeg ikke lenger har driftsstopp og dermed sparer en hel del penger, forklarer Purić entusiastisk. Hvis det også er behov for service, for eksempel kalibreringer som pålegges av testsenteret hvert år, kommer det en Fronius-tekniker som raskt utfører dette på stedet.
For mer informasjon se: www.fronius.com
Kilde: Fronius