3D-metallprinting på norsk vis
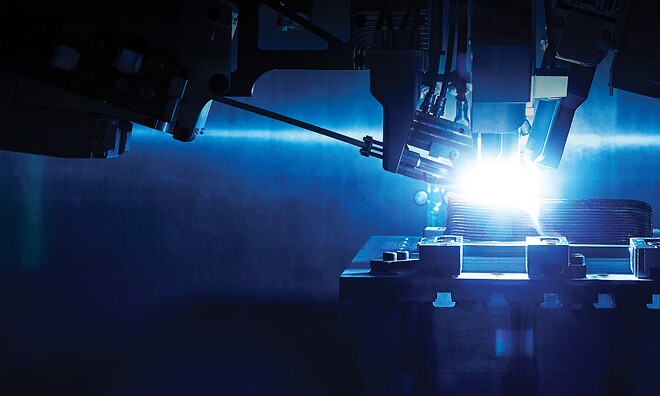
Mens det norske markedet for additiv produksjon (AM) lenge dreide seg om modellbygging og prototyper i polymerer har det i de siste årene vært en positiv utvikling innen bruk av additiv produksjon i metall. I denne artikkelen ser vi på hvorfor det har tatt så lang tid å komme i gang med metallprinting i Norge og hvem det er som nå leder an.
Etter at det ble funnet olje på norsk sokkel desember 1969 har mye av den norske industrien handlet om nettopp olje og gass. Denne sektoren er mer enn syv ganger større enn all annen industri til sammen i Norge. Dette er greit å vite når man ser på utviklingen av metallprinting i landet.
Akademia i forkant
På slutten av 1990-tallet var forskningsinstituttet SINTEF i gang med å forske på 3D-printing med metaller. Dette var tidlig ikke bare sett med norske øyne, men også globalt. De akademiske miljøene i Norge har siden forsket en god del innen additiv produksjon og Norges forskningsråd har siden 2004 gitt støtte til 292 AM-prosjekter.
SINTEF er pådriver sammen med NTNU i Trondheim der de disponerer felles AM-lab, og jobber aktivt med prosjekter sammen med industrien.
Også hos Universitetet i Agder og Mechatronics Innovation Lab (MIL) samt Forsvarets Forskningsinstitutt (FFI) printes det i metall. Sistnevnte har laget en rapport om dagens bruk av teknologien og forskningsfrontene samt prognosene frem mot 2045.
Mye aktivitet i akademia, men hvorfor har produksjonsbedriftene i landet har ventet med å omfavne AM metallprinting?
Henger etter
Skal vi finne årsaken må vi se vi på sammensetningen av norske industribedrifter og hva de produserer. Her ser vi mange små virksomheter, 90 prosent av alle bedrifter som produserer metallvarer har mindre enn 50 ansatte. Små bedrifter som har stor aktivitet inn mot oljenæringen har liten eller ingen påvirkning på hvordan oljeindustrien utvikler seg.
De fleste underleverandørbedriftene mottar ofte ordre med mange varianter og små serier, altså hovedsakelig stykkproduksjon, noe som skulle tale for bruk av AM-teknologi, men hvorfor har ikke denne teknologien blitt like utbredt i Norge slik som i andre europeiske land?
Svaret er at det i all hovedsak er oljeindustrien i Norge som har ligget etter, men det er nå i ferd med å endre seg.
Suksess med titanprinting
Før vi ser dypere på oljeindustrien i Norge må vi nevne industrisuksessen Norsk Titanium som klart skiller seg ut innen norsk metallprinting, og som har vist vei innen additiv produksjon i titan globalt sett. Et lite team av norske forskere og ingeniører dannet i 2004 selskapet Norsk Titanium. Fra mer enn ti år med materialvitenskapelig forskning og prosesskontroll kom de frem til sin prosess: «Rapid Plasma Deposition». Kort fortalt er det når titantråd smeltes i en inert atmosfære av argongass og bygges nøyaktig og raskt opp i lag til en nesten nettoformet del. Det Norsk Titanium fikk til gjennom sin prosess var å åpne opp markedet for additivt produserte titankomponenter til flyindustrien. Det er imponerende, særlig når man vet at flyindustrien har noen av de strengeste kravene til kvalitet. Norsk Titanium har flere patenter innen AM-teknologi og er sertifisert etter AS9100C, AS9100D og NORSOK M-650. Senere etablerte bedriften produksjon i USA og i 2021 gikk selskapet på børs.
NORSOK-bøygen
Selv om Norsk Titanium er en norsk suksesshistorie innen metallprinting hovedsakelig for flyindustrien, er størsteparten av industrivirksomheten i Norge rettet mot oljesektoren, og det er også her reglene settes.
For å levere kritiske komponenter til oljenæringen må leverandørene blant annet tilfredsstille kravene satt i NORSOK-standardene.
Akronymet NORSOK står opprinnelig for «norsk sokkels konkurranseposisjon» og ble introdusert i 1994 for å kutte kostnader og forbedre konkurranseevnen på norsk kontinentalsokkel.
NORSOK-standardene er utviklet av norsk petroleumsindustri for å sikre tilstrekkelig sikkerhet, verdiskaping og kostnadseffektivitet for utviklingen og driften av denne industrien. Videre er NORSOK-standarder så langt som mulig ment å erstatte oljeselskapenes spesifikasjoner og fungerer som referanser i myndighetenes regelverk.
Det er mye arbeid som ligger bak beskrivelsene i NORSOK, og når det gjelder AM-teknologi har det tatt mange år å få på plass retningslinjer for additiv metallproduksjon til bruk i petroleumsindustrien. Vi kommer tilbake til NORSOK litt senere.
Så langt så godt
Sammenliknet med andre land i Europa har det norske AM-miljøet få industrielle metallprintere. Eksempelvis bygget den tyske underleverandørbedriften FIT AG ny fabrikk i 2016, den hadde da 30 industrielle metallprintere og like mange industripolymerprintere. På samme tid i Norge hadde man to metallprintere innen akademia og to i industrien.
Det til tross, det innovative industrikonsernet Tronrud Engineering AS hadde allerede i 2010 skaffet seg en EOS M280 metallprinter som de brukte til å lage deler til maskiner som de utviklet og bygget for sine kunder. I 2017 hadde bedriften virkelig fått fart på metallprinteren sin og serieproduserte patentert og egenutviklede lyddempere i titan.
Tronrud var den første kommersielle bedriften i Norge som tok i bruk industriell metallprinting. Senere har selskapet investert i nok en EOS M290 og en EOS Formiga. Nå tilbyr selskapet 3D-printing til eksterne kunder.
Underleverandørbedriften Promet AS var den andre industribedriften som investerte i industriell metallprinting, de fikk sin SLM 280 HL i desember 2014.
Promet har nesten utelukkende kunder innen oljeindustrien og driver med døgnkontinuerlig stykkproduksjon på CNC-frese- og dreiemaskiner.
Bedriften, som holder til like utenfor Stavanger, arrangerte i 2015 åpent hus der fagfolk fra oljeindustrien og akademia møtte opp. Promet hadde mange møter med aktørene i oljenæringen, alt fra oljeselskap til underleverandører, og fikk til et godt samarbeid med blant andre UiS (Universitetet i Stavanger). UiS deltok i et prosjekt, ledet av industribedriften EnergyX, som resulterte i at Norges første kjente nedstrømsverktøy for rensing av rør ble 3D-printet i Inconel 718 hos Promet AS.
Dette var i 2016, før noen AM-prosesser var beskrevet i noen standard for oljeindustrien i Norge, så det var kunden BP som godkjente verktøyet for bruk i felt. Veien videre for Promet ble lang, og fordi NORSOK ikke hadde AM-prosesser for metall beskrevet ble det lite oppdrag fra oljesektoren. Bedriften ga etter noen år opp og solgte SLM-maskinen sin.
Gjennombruddet
I 2015 tok det tekniske fagbladet Maskinregisteret initiativ til å få aktørene i oljeindustrien på banen for å få aksept for 3D-metallprinting. Det nederlandske konsulentfirmaet Berenschot ble invitert til å lede et prosjekt som hadde som mål å demonstrere metallprinting for alle aktørene i verdikjeden, fra 3D-modell til ferdig produsert, testet og dokumentert applikasjon.
Den 7. september 2016 startet et pilotprosjekt innen additiv produksjon. Dette var det første prosjektet i sitt slag som inviterte hele den norske industrien, akademia og det offentlige til felles løft på tvers av industriklynger.
Det ble gjennomført tre seminarer i samarbeid med NTNU, UiS (Universitetet i Stavanger) og Robotek AS.
Oppslutningen var god, entusiasmen større, men etter de gjennomførte seminarene var det tydelig at norsk oljeindustri ikke var klar for å 3D-printe med metall.
Onno Ponfoort, AM-leder hos Berenschot, ville vite hva som sto i veien, han hadde jo tross alt vist hva man hadde fått til i Nederland, kunne det være så veldig vanskelig?
Ja, NORSOK var i veien, og Ponfoort ble oppmuntret til å lage et industriprosjekt for nettopp å få hull på byllen, og få AM-teknologien beskrevet for oljenæringen. Han kontaktet sentrale aktører som energiselskapet Equinor og klasseselskapet DNV for å sondere terrenget og fikk i gang en dialog som endte med at man i januar 2018 startet et «Joint Industry Project» som hadde som mål «å standardisere og optimalisere kvalifiseringsprosesser for additiv produksjon (AM), redusere kostnadene og miljøpåvirkningen av produksjon gjennom AM, og muliggjøre bruk av AM i relevante designapplikasjoner i energi- og maritim sektor». I prosjektets konsortium deltok Equinor, BP, Total, Shell, Kongsberg, Aidro, OCAS/ Guaranteed (spin-off fra Arcelor Mittal), Ivaldi Group, TechnipFMC, Siemens, Voestalpine, Vallourec, SLM Solutions, Additive Industries, Quintus Technologies, HIPtec, IMI CCI, Advanced Forming Research Centre of the University of Strathclyde, Immensa Lab og Sandvik.
Dette ble et gjennombrudd for oljeindustriens satsing på metallprinting i Norge og starten på en lang reise videre.
Equinor som digital pådriver
Med flere AM-prosesser nå beskrevet for petroleumsindustrien kunne energiselskapet Equinor gå i gang med å definere hvorfor man skulle 3D-printe komponenter i metall. Det var mye snakk om hvor fantastisk teknologien var, men var det egentlig noen gevinster å hente?
- Fra Equinor sitt perspektiv så vi på hva AM-teknologien kunne gjøre for sluttbrukerne, hva er det vi løser med 3D-printing, uttaler Brede Lærum, leder av AM Centre of Excellence, AM-satsingen til energiselskapet Equinor.
Lærum har i mange år vært en ivrig pådriver for additiv produksjon og er en tydelig profil innen AM-miljøet i Norge. Han mener det er flere grunner til å benytte teknologien, også utenfor oljeindustrien:
- 3D-printing er en teknologi som utelukkende er basert på digital informasjon. Uten en 3D-modell ingen 3D-print. Følger vi det digitale sporet finner vi fort ut at reservedeler, som er svært kritiske innen oljeindustrien og andre industrier, ikke nødvendigvis må være fysiske og ligge på et lager. Vi kan ha digitale reservedeler og produsere dem når vi trenger dem, forteller Lærum.
Han tegner opp et bilde der alle aktører har digitale tegninger, som sendes til og fra hverandre ved behov, og der alle kan tjene penger på sin innsats underveis frem til ferdig produsert del.
- Hvis alle som har reservedelslager begynner å regne på kostnadene ved å ha et slikt lager vil de finne ut at det er veldig store summer plassert i noe som ikke er i bruk. Ved digitale varelager kan vi oppnå store gevinster, mener Lærum.
Han tenker på miljøavtrykket men også tid til marked.
- Så klart får vi et bedre miljøavtrykk når vi ikke behøver å «overprodusere» reservedeler som ikke blir brukt, men det er en annen dimensjon i at vi kan produsere lokalt. Ikke bare sparer vi transportkostnader og miljøutslipp, men vi får løsninger levert raskere til der de trengs som mest, for AM-teknologien har store fordeler når det gjelder tid. En digital del kan flyttes på sekunder til der hvor delen trengs. Selv om man med dagens teknologi må beregne en del timer på å printe en metallkomponent er AM-teknologien konkurransedyktig sammenliknet med tradisjonelt fremstilt del, når man tar høyde for alle oppsidene. Dette lover godt for mer bærekraft ikke bare i vår industri, men i alle andre også, mener Lærum, som legger til at Equinor ikke er alene om AM-satsing:
- Vi har etablert et samarbeidsprosjekt med i alt åtte energiselskaper. Målet vårt er å lage et helt økosystem og utvikle nye metoder for å hente ut gevinsten ved bruk av AM-teknologi og digitale reservedelslagre. Dessuten vil vi at de positive resultatene vi oppnår sammen, ved å benytte AM-teknologien, også kan nå andre industribransjer.
- Slik jeg ser det har vi fire tydelige fordeler ved bruk av AM:
- Reduksjon av kostnader
- Vesentlig redusert miljøfotavtrykk
- Økt leveringssikkerhet
- Lokal verdiskaping
- Sistnevnte er viktig, og blir et momentum, for hvis vi kan fremstille lokalt og selge globalt, alt mulig, ja eksempelvis som med musikk som kjøpes på Spotify, vil hele verden få et løft på flere plan, og det største kanskje innen bærekraftforbedring, understreker Brede Lærum.
De gode eksemplene
Fieldmade – best i felt
Ut av Forsvarets forskningsinstitutt kom det i 2016 et oppstartselskap som fikk navnet Fieldmade. Som firmanavnet antyder handler det om 3D-printing i felt, og ikke unaturlig var det initiale fokuset på det norske Forsvaret.
Fieldmade kom raskt med i Forsvarets feltøvelser og beviste at det var fullt mulig å produsere reservedeler til stridsenheter på sjø og land.
Konseptet Fieldmade jobber ut fra er en mikrofabrikk i en spesialbygget container (NOMAD) som inneholder alle innsatsvarer og maskiner som trengs for å fremstille funksjonelle deler rett fra en ferdig 3D-modell, eller ved reverse engineering ved hjelp av 3D-skanning. I begynnelsen printet man i polymer, men ambisjonene ble større og ønsket var å kunne printe metall med fullskala industriprinter.
I samarbeid med DMG MORI bygget Fieldmade om en Lasertec 30 til å tåle rystelser og vibrasjoner som oppstår under transport av containeren uten at det skulle påvirke kvaliteten på de printede delene. Tester med container på lastebil kjørende i terreng resulterte i at man i dag har et velfungerende system for metallprinting i felt. Ryktene sprede seg raskt og Fieldmade fikk oppmerksomhet både i og utenfor Norge.
- Vi fikk henvendelser fra NATO og andre som ville vite mer, og et av temaene som tidlig ble drøftet var IP-rettigheter, forteller Christian Duun Norberg, grunnlegger av Fieldmade og Fieldnode.
Utfordringene ble hvem har rett til å printe hva og hvordan verifisere 3D-modellene og ikke minst hvordan lage et sikkert system.
- Digitaliseringen er jo nøkkelen i 3D-printingen. Man kan sende 3D-filer hvor som helst, men det er mange faktorer som spiller inn og dermed lå veien åpen for å etablere et nytt selskap; Fieldnode, sier Duun Norberg.
Fieldnode leverer et digitalt lagerøkosystem som gir mulighet for lokal produksjon av reservedeler, reduserer lageroppbygging og forbedrer driftseffektiviteten. Løsningene selskapet leverer vekket interessen også i oljeindustrien.
- Vi har et godt samarbeid med energiselskapet Equinor, som utfordret oss med å gi oss et feltoppdrag. De ønsket å se om det var mulig for oss å demonstrere 3D-teknologien på verftet hos Aker Solutions på Stord, Vestland fylke, forteller Duun Norberg.
Opprinnelig fikk Fieldmade en avtale som skulle gå fra oktober 2022 til oktober 2023, men den er nå forlenget.
- I løpet av 12 måneder har det vært >380 unike bestillinger og >6000 produserte deler, som var langt over forventet antall deler, og nå har Equinor utvidet avtalen til mai 2023, legger Duun Norberg til.
Fieldmade har drevet frem mobile AM-løsninger også i samarbeid med Mark3D.
- Hos Fieldmade tror vi på å flytte grensene for hva som er mulig, selv når det innebærer å kaste vår NOMAD LW ut av et RAF-fly.
Resultatene er intet mindre enn ekstraordinære, forteller Duun Norberg og fortsetter:
- Nylig satte vi NOMAD LW på den ultimate testen ved å slippe den fra et RAF-fly. Men det er her magien skjer: Innen bare tre minutter etter at den ble pakket ut, var den satt opp og i full drift. Ingen justeringer, ikke noe oppstyr. Klar til å produsere sluttbrukerdeler fra det integrerte Markforged Marktwo-systemet.
Hva er hemmeligheten?
- Våre dedikerte ingeniørers oppfinnsomhet. Våre systemer og løsninger, brukt på tvers av NOMAD-serien, absorberte svimlende 10 g kraft under luftfallet, og sørget for at kabinettet og dets innhold forble intakt og klart til printing, svarer Duun Norberg, og legger til:
- Sammen med det integrerte UPS-systemet betydde denne bragden at vi kunne printe ut uten det umiddelbare behovet for en strøminfrastruktur. Vi trenger ikke finne opp hjulet på nytt, det handler om å ta innovasjon til nye høyder og produsere der det er mest behov for det.
Additech først sertifisert med PBF-LB
Den 26. april 2023 mottok 3D-printspesialisten Additech AS og er med det først i verden som DNV-kvalifisert BPQ i titan grad 5 (Ti-6AI-4V) for PBF-LB-teknologi (Powder Bed Fusion–Laser Beam).
- Denne sertifiseringen fungerer som en indikasjon på Additechs sterke posisjon i den norske AM-industrien for energi, olje og gass og maritim sektor, uttaler Anders Helland, CEO i Additech AS.
Additech er en av pådriverne innen industriell AM i Norge og kjører utdanning av egne folk og andre som har behov for økt kompetanse. Til dette benytter selskapet CADS Additive’s AM-Studio suite.
- For Additech, som er en del av det norske katapult-programmet, som har som mål å støtte innovasjon i små og mellomstore bedrifter i spesifikke områder av landet, spiller også utdanning en stor rolle i selskapet. Vi ser det enorme potensialet til AM, og ønsker å etablere vår tankegang om «Learning by Doing» i industri og universitet, sier Helland.
Redusert ressursbruk
Aker Solutions og partnerne Aker BP, F3nice og Additech har tatt et viktig skritt mot en mer sirkulær økonomi. Et pilotprosjekt for additiv produksjon viser det store potensialet for å spare ressurser ved å legge avfall til produksjonsprosessene. Partnerskapet er 3D-printrørhengerbeskyttere for undervannsbrønner med en pulverisert blanding av resirkulert skrap hentet fra Aker Solutions verksteder i Tranby, Norge.
Jobben med å konvertere metallavfall til tilsetningspulver ble overlatt til spesialistene ved F3nice. De behandlet råmetallrester og leverte dette til Additech som printet delene. Resultatet er redusert energiforbruk, transport og redusert skrap, noe som minsker miljøfotavtrykket.
NAM – først sertifisert med LMD
NAM (Nordic Additive Manufacturing) har sitt utspring fra innovasjons- og industrimiljøet på Raufoss, i Innlandet, og er en av de ledende aktørene innen industriell 3D-printing med LMD (Laser Metal Deposition) i verden. I tett samarbeid med Sintef Manufacturing, og nøkkelkunder som Equinor og Nammo, har man nå sertifisert produksjonsprosessen i henhold til DNV- og internasjonale standarder.
- Med en DNV-kvalifisering på LMD, er NAM første i sitt slag i verden og setter bokstavelig talt en ny standard innen denne teknologien. Dette setter NAM i en unik posisjon og baner vei internasjonalt, uttaler Sture H. Sørli, daglig leder i NAM.
NAM blir å finne på Formnext 2023 i Frankfurt og stiller ut sammen med den italienske materialleverandøren Mimete i hall 12, stand D48.
Årdal først
Årdal Maskinering AS på Nærbø, i Rogaland, var først og eneste i verden med Mazak Integrex i500-AM med tre meter dreielengde og diameter på Ø300 mm. Maskinen kan ta større dimensjoner, men da ikke så lange på grunn av brille. Denne maskintypen og maskinen er stor, den veier 31 tonn, og det spesielle er at den i tillegg til å være et 5-akset frese-dreiesenter har den også mulighet for additiv produksjon gjennom et eget laserhode. Prosessen, som heter DED (Directed Energy Deposition), og er beskrevet for oljeindustrien, består av å smelte på material i pulverform via en kraftig laser, hvor type laser som er i bruk bestemmer hvilket material som kan kladdes.
Maskinen ble levert i 2020, men etter forsinkelser på grunn av pandemi kom man først i gang med å benytte AM-prosessen i 2022. Nå utfører Årdal Maskinering vellykte reparasjoner i eksotiske legeringer.
- Vi har blant annet fått oppdrag fra kunde hvor vi har reparert ødelagte og slitte deler, samt støpte produkter fra Kina, som ikke har vært i henhold til spesifikasjoner, forklarer Frode Hegle, kvalitet og HMS-leder hos Årdal Maskinering AS og legger til:
- I et annet oppdrag leverte kunden en del på 3100 mm hvor en gjenge var revet. Vi fjernet gjengen, la på nytt materiale og maskinerte ny gjenge i henhold til spesifikasjoner. Resultatet var en suksess, kunden unngikk å vrake delen. Dermed slipper de lang leveringstid og mulig lang transport ved ny del, i tillegg til at materialforbruket reduseres, og det er bærekraft i praksis, mener Hegle.
Aarbakke med WAAM
Aarbakke AS, på Bryne, i Rogaland, er Norges største maskineringsbedrift med over 300 ansatte. Her er 70 prosent av oppdragene nye deler, altså mye stykkproduksjon. Kundene er innen oljesektoren. Spesialiteten er avanserte og komplekse komponenter i eksotiske legeringer, mye i Inconel, Superduplex og titan. Spesialitet er også kladding i de samme legeringene, noe de gjør robotisert. Erfaringene fra denne aktiviteten har ledet til at bedriften nå satser på WAAM.
- Vi har stor tro på WAAM, som er beskrevet for oljenæringen, og vi har god erfaring med kladding, så nå jobber vi med å igangkjøre Norges første anlegg som vi har bygget etter egne spesifikasjoner, sier Inge Brigt Aarbakke, bedriftseier og forretningsutvikler i Aarbakke AS, og legger til:
- WAAM benytter tråd, den er lettere tilgjengelig enn metallpulver og prosessen er billigere enn andre metallprosesser. Faktisk er råvaren billigere enn pulver. Byggehastigheten er rask og vi tror dette vil bli en ledende prosess både for reparasjoner og for nye komponenter innen oljeindustrien.
Enorm mulighet
Det norske rederiet Wilhelmsen og det tyske industrikonsernet thyssenkrupp har med sitt 3D-printingpartnerskap som visjon å transformere forsyningskjeden for marine og offshoredeler, erstatte eksisterende ineffektive og rigide forsyningskjedeprosess med en tilpasset, on-demand og mer effektiv prosess for 3D-printing.
Gjennom en unik digitaliserings- og sertifiseringsprosess produseres deler på forespørsel, uten å måtte gå gjennom de tidkrevende og kostbare lagrings-, frakt-, toll- og mottaksprosessene. AM endrer den kostbare og tidkrevende reservedels status quo, slik at egnede komponenter kan produseres nær fartøyets plassering med kort ledetid.
- Besparelsene fra reduserte kostnader, tid og miljøavtrykk gitt av 3D-printing, digital lagerbeholdning og lokalisert produksjon av maritime reservedeler, er en enorm mulighet for våre kunder til å være foran sine rivaler, sier Hakon Ellekjaer, tidligere leder for 3D Printing hos Wilhelmsen, nå Chief Commercial Officer hos Pelagus
3D, et nytt joint venture mellom ThyssenKrupp og Wilhelmsen.
Kvalitetssikring
Norske DNV og svenske Siemens Energy er i ferd med å ta additiv produksjon inn i neste modenhetsfase. Siemens Energys eksperter i Finspång, Sverige, har utviklet den første generasjonen av AM Cockpit-plattformen som gir automatisert, pålitelig kvalitetskontroll av 3D-metallprintprosessen. På sin side har DNV utviklet plattformen Independent Quality Monitor (IQM) – en kundeportal som kontinuerlig kvalitetssikrer digitale løsninger.
Ved å kombinere disse to løsningene kan DNV lansere en kommersiell løsning for AM-industrien – som sikrer at 3D-printede deler enkelt kan sammenlignes med en såkalt godkjent masterprint. Kombinasjonen gjør også automatisert og ekstern prosess-sertifisering mulig.
Satsing i Nord-Norge
Sommeren 2023 startet AM North AS med metallprinting i Hammerfest i Nord-Norge. Byen ligger på 70,7 grader nord og metallprinteren som står her er kanskje verdens nordligste i sitt slag.
Metallprinteren som AM North har investert i er en DMG MORI Lasertec 30 Dual SLM. Den er i utgangspunktet tenk å lage deler til oljenæringen, men i AM North har man større vyer.
- Vår lokasjon er perfekt på flere måter. Ikke bare er vi fysisk lokalisert i det samme bygget som reservedelslageret til oljeproduksjonsskipet Johan Castberg, til Polarbasen kommer alt av sjøgående kunder også utenfor oljenæringen. Vi snakker om fiskeri, oppdrett og alle andre maritime aktører. Dessuten er vi nær gruvedrift og andre industriaktiviteter i regionen. På sikt vil vi også se ut av regionen og landet, vi tror på å bli en global aktør, uttaler Jan-Inge Kongsbak, daglig leder i AM North AS.
Mer satsing i nord
Industrial AM AS, i Mo i Rana i Nordland, har bestemt at de skal bli en fortrukket leverandør av industrielle komponenter i metall ved bruk av additiv produksjon. Selskapet eies av Momek Robotics, Testpartner og Kunnskapsparken Helgeland. Planen er å utvikle en komplett verdikjede med 3D-skanning, konstruksjon, 3D-printing, maskinering, varmebehandling, testing og sertifisering. Industrial AM skal samarbeide med ledende bedrifter, forsknings- og utviklingsaktører innen moderne fabrikasjonsteknologi og 3D-printing.
Equinor og Aker BP går inn og støtter etableringen basert på et behov for denne type leveranser fra Nord-Norge. For operatørene handler det om redusere lagerhold, rask leveringstid, kortreiste leveranser, lavere CO2-avtrykk og tilgjengelig kompetanse og kapasitet.
Egen AM-forening
Norwegian Additive Manufacturing Cluster (NAMC) ble etablert i 2022. Det er en forening som har som mål å være det nasjonale nettverket for additiv produksjon i Norge. Nettverket er åpent for bedrifter og organisasjoner fra alle bransjer, samt utdannings- og forskningsinstitusjoner. Nettverket søker å fremme utviklingen av et økosystem og kunnskap rundt AM i Norge, koble sammen relevante interessenter på tvers av bransjer, og stimulere til vekst, innovasjon og nye bærekraftige løsninger.
Første konferanse
I mars 2023 arrangerte Norwegian AM sin første konferanse og vertskapet var SINTEF og NTNU i Trondheim. Målet for konferansen var å presentere eksempler på bruk av additiv produksjon i industriell anvendelse. Flere av AM-teknologiene er i ferd med å få fotfeste i Norge i sektorer som helse, forsvar, maritim sektor, vareproduksjon og oljesektoren. Til stede på konferansen deltok aktører fra næringsliv, offentlige institusjoner og akademia. Selskaper som eksempelvis Equinor, Wilhelmsen, Ivaldi, Vår Energi, Kongsberg Maritime og Lærdal Medical var blant et 20-talls foredragsholdere som fortalte hvordan de utnytter mulighetene som ligger i additiv produksjon. Med 170 deltakere på første forsøk må man si det ble en suksess.
Stilte ut på Formnext
Norwegian Additive Manufacturing Cluster (NAMC) stilte ut på den nordiske partnerpaviljongen på Formnext 2023 i Frankfurt.
- NAMC vil tilstrebe et godt partnerskap både på AM Summit-samarbeidet og Formnext-utstillingen og etablerer dette for et langsiktig gjensidig verdifullt samarbeid. På programmet hadde vi i alle fall et par gode historier å dele, uttaler Jan Tore Usken, leder av Norwegian AM.
Blant annet deltok Equinor med deres ledetid og kostnadsreduksjoner. Deres AM Center of Excellence-team var tilstede med noen deltakere på Formnext.
Fieldnode presenterte sitt banebrytende supply chain management med digitale lagersystemer. Et massivt samarbeid med ConocoPhillips, Equinor, Shell, TotalEnergies, Vår Energi og Woodside.
AMMA-konferansen FFI
AMMA 2023, som arrangeres av FFI den 3. november, for det syvende året. Målet er å tilby en plattform for presentasjon av nyere FoU-fremskritt innen additiv produksjon, og for å samle fagpersoner fra Forsvaret, statlig forsvars-FoU, industri og akademia.
Elefanten i rommet - utdanning
Helt siden man startet med metallprinting har det vært et skrik om hjelp innenfor opplæring og utdanning av nok og riktig personell til å utnytte potensialet som ligger i AM metallprinting. Det gjelder i hele verden, og selv om man i noen land ligger foran gjennomsnittet har man i Norge ligget etter.
Nå som oljenæringen har åpnet for metallprinting skorter det like fullt på konstruktører som er utdannet innenfor additiv produksjon. Kundene i oljeindustrien har få spesialister innen AM metallprinting som vet å bestille metallprinting, og de enkelte aktørene som produserer industriell metallprinting sliter med rekruttering av konstruktører og operatører. Mange AM metallprosjekter starter med reverse engineering eller overføring av tradisjonell teknologi til AM. Det er et stykke igjen før man har på plass «allmennkunnskap» om «design for AM».
Selv om det ikke er noe utdanningsløp innenfor AM fra yrkesskole via fagskole, høyskole og til universitet, som kan gi en egen yrkestittel i AM-teknologi, er det flere initiativ fra enkeltaktører. Nedenfor er noen eksempler:
Mechatronics Innovation Lab (MIL) ble etablert med det formål å øke virksomheters konkurransekraft gjennom bruk og forståelse av ny teknologi. Gjennom involvering og tilskudd fra privat næringsliv og det offentlige har MIL bygd opp Norges største og heftigste techlab. Dette samarbeidet mellom industri, akademia og offentlig sektor har gjort at MIL i dag er en teknologisk hub av internasjonal standard.
MIL tilbyr teknologi, testutstyr og kompetanse for innovasjon innen mekatronikk og tilhørende fagdisipliner, slik som robotikk, sensorikk, autonomi, kunstig intelligens, virtuell virkelighet og industriell 3D-print i alle typer materialer. Som partner i Future Materials katapulten deltar MIL med utstyr og kompetanse innen materialutvikling.
MIL er en del av den nasjonale infrastrukturen for innovasjon, pilot-testing, eksperimentell utvikling av industrielle produkter, systemer og tjenester for introduksjon i markedet.
På linje med det MIL tilbyr i Grimstad, på Sørlandet, tilbyr Norwegian Technology Catapult Center (MTCN) på Raufoss, i Innlandet, additiv og hybrid produksjon med Laser Metal Deposition-teknologi (LMD) som nå er tilgjengelig gjennom katapulten, herunder lasersveising (wire, pulver, laser), laserherding og laserskjæring. Her kan man få hjelp til å videreutvikle, simulere og teste produksjonslinjen før man kjører i gang fullskalaproduksjon i egne lokaler.
NTNU Gjøvik, i Innlandet, kjører kurs innen AM i polymer og deltar i prosjekter med industrien.
SINTEF har laget en egen AM-veileder for industrien. Den beskriver hvordan bedrifter kan produsere og vedlikeholde produkter med reduserte kostnader, svinn og materialforbruk.
Steinar Killi, professor ved Arkitektur- og designhøgskolen i Oslo (AHO) har skrevet boken «Additive Manufacturing: Design, Methods, and Processes» på engelsk.
Dette er en lærebok for kandidatstudenter innen design, ingeniørfag, datavitenskap, markedsføring og teknologi, og også for de som ikke er studenter, men er nysgjerrige på og interessert i hva 3D-printing virkelig kan brukes til.
Et av få selskap innen AM-engineering i Norge er Korall Engineering AS som er et designingeniørfirma som er en del av StartupLab Bergen, medlem av GCE Ocean Technology Cluster, som bruker de nyeste avanserte designoptimaliseringsteknologiene. Teamet deres automatiserer arbeidsflyt for produktdesign for å redusere prosjektering og ledetider og redesigner eksisterende industrielle produkter gjennom bruk av kunstig intelligens for å redusere materialavfall og produksjonskostnader, øke effektiviteten og redusere miljøpåvirkningen.
Flere av produsentene av AM-maskiner tilbyr opplæring innen AM-faget til både konstruktører, produksjonsledere, operatører og bedriftsledere, noe de fleste av de norske kundene innen metallprintingmaskiner har benyttet seg av.
Næringsforeninger, utdanningsmiljøer og bedrifter i de ulike regionene har gjennom de siste årene arrangert samlinger og seminarer for å bevisstgjøre alle aktørene i industrien om potensialet innenfor AM. Numerisk Bruker Forening inkluderer AM-presentasjoner i sine Brukermøter.
Norsk Industri er aktive gjennom sitt bransjeforum «Forum for maskinering og additiv tilvirkning», og i mars 2023 arrangerte Norsk Industri og Offshore Norge dialogmøte om 3D-printing i fremtidens forsyningskjeder i energisektoren arrangert hos Vår Energi i Stavanger. Der deltok 100 personer.
Konklusjon
Til tross for at akademia i Norge var tidlig ute med å printe i metall tok det relativt lang tid å etablere AM metallprinting på industriell basis. Sett med historiske øyne er det ikke så underlig, all den tid oljeindustrien, som står så sterkt i landet, setter premissene for hvordan komponenter skal fremstilles. Uten retningslinjer for å produsere godkjente og sertifiserte deler med metallprinting er det ikke så rart at investeringene lot vente på seg.
Det at det nå finnes flere AM-prosesser beskrevet for oljeindustrien gjør at industrien for alvor er kommet i gang med metallprinting. Nye AM-miljøer er under planlegging flere steder i landet.
At man har fått på plass en egen AM-forening bidrar til at alle aktørene i AM-miljøet i Norge får raskere utvikling på flere plan. Samarbeid på tvers av industriklyngene fører gjerne til positive synergier.
De få men unike eksemplene presentert i denne artikkelen forteller en historie om at industrien i Norge satser der det er behov og muligheter, og kun tiden vil vise om man i kongeriket kan bli like store på additiv produksjon som konkurrentene er i andre land.
Kommentar
Denne artikkelen ble skrevet på oppdrag for MetalAM og publisert i deres magasin Vol. 9 No. 3 Autumn 2023, som ble delt ut på Formnext-messen i Frankfurt i november 2023. Artikkelen finnes også digitalt på www.metal-am.com
I tiden etter messen har det skjedd en del nye ting i Norge, både hva gjelder maskininvesteringer og flere AM-arrangementer. I tillegg bygges det blant annet opp et utdanningsmiljø på NTNU i Trondheim og allerede undervises det her i «Additiv tilvirkning med avanserte legeringer».
Et nytt AM-miljø på Jæren er i ferd med å etableres og AM-plattformen og forretningsportalen Locat3D blir et spennende tilskudd til det norske AM-miljøet som i disse dager er på hurtig fremvekst.