3D-printet damaskusstål
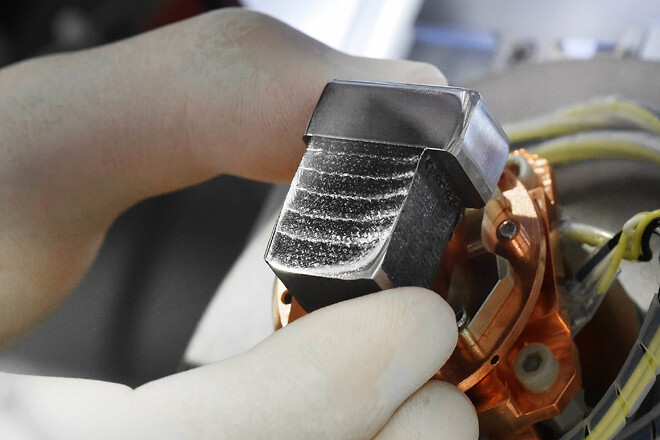
Et komposittmateriale med metallag av varierende hardhet kan produseres gjennom smart temperaturvariasjon.
Materialet har et legendarisk rykte. Damaskusstål er hardt, men seigt fordi det består av lag av forskjellige jernlegeringer. I gamle tider var dette materialet spesielt egnet for sverdblad. Et team fra Max-Planck-Institut für Eisenforschung i Düsseldorf og Fraunhofer Institute for Laser Technology i Aachen har utviklet en prosess som gjør at denne typen stål kan produseres lag for lag i en 3D-printer. Hardheten til hvert enkelt lag kan justeres spesifikt. Slike kompositter kan være av interesse for luftfartkomponenter eller verktøy produsert med 3D-printere.
Seigt og hardt
Tidligere var smedene i stand til å påvirke egenskapene til jernlegeringer bare ved å justere karboninnholdet. De fikk enten et mykt, men seigt eller et hardt, men sprøtt stål. Spesielt for sverd var det nødvendig med et seigt og hardt materiale slik at bladene ikke ville knekke eller måtte rettes ut midt i en kamp.
Keltiske smeder kombinerte forskjellige jernlegeringer (kanskje i utgangspunktet bare for å resirkulere det verdifulle jernet) og fikk dermed materialet som senere ble kjent som damaskusstål eller damask. Det skylder navnet sitt til handelssenteret der komposittmaterialet av orientalsk opprinnelse kom inn i Europa. Mens indisk og arabisk damask ble skapt av en sofistikert smelteprosess, utviklet europeiske smeder kunsten å brette to legeringer i mange tynne lag. Den lagdelte strukturen av damaskusstål kan vanligvis gjenkjennes ved et karakteristisk stripemønster.
Krystallstrukturen kan endres med laser
Selv om det for tiden er jernholdige legeringer som er både harde og seige, er de ofte ikke spesielt laget for 3D-printprosessen, og utnytter dermed ikke fordelene med denne produksjonsteknikken fullt ut. Forskere ved Max-Planck-Institut für Eisenforschung (MPIE) og Fraunhofer Institute for Laser Technology har nå utviklet et stål som bare består av et enkelt utgangsmateriale, men som består av vekslende harde og duktile lag - en slags Damaskusstål, gjennom 3D-print. "Vi har lykkes med å modifisere mikrostrukturen til de enkelte lagene under 3D-print, slik at den endelige komponenten har de ønskede egenskapene - og alt dette uten etterfølgende varmebehandling av stålet", sier Philipp Kürnsteiner, postdoktorforsker ved MPIE.
3D-printere for additiv produksjon (den tekniske betegnelsen for denne prosessen) har blitt standard i mange industrisektorer i løpet av få år. De er i stand til å produsere plast så vel som metalliske komponenter. Den respektive legeringen tilsettes som et fint pulver, smeltes av en laserstråle og påføres gjentatte ganger lag for lag for å danne den ønskede komponenten. De siste årene har det blant annet blitt produsert dyser til flymotorer ved bruk av denne additive fremstillingsmetoden, også kjent som laserkladding.
Laserstrålen gjør det mulig å ikke bare smelte det respektive materialet, men også å varme opp det øverste laget av det allerede resolidiserte metallet. Dette er nøyaktig hva teamet til Max Planck-forskerne i Düsseldorf brukte for å endre krystallstrukturen til stålet i individuelle metallag - og dermed påvirke de mekaniske egenskapene uten å endre den kjemiske sammensetningen.
Varmes opp igjen
Pauser i trykkeprosessen tillater dannelse av herdende utfellinger
De utviklet en legering bestående av jern, nikkel og titan. Først er denne legeringen relativt myk.
- Under visse forhold dannes små nikkel–titan mikrostrukturer. Disse, såkalte utfellinger, herder materialet, forklarer Kürnsteiner, og legger til:
- Når de utsettes for mekanisk belastning, hindrer de bevegelsen av forskyvninger i krystallgitteret som er karakteristisk for plastisk deformasjon.
For å være i stand til å skape nikkel–titanstrukturene, avbryter forskerne trykkprosessen i en viss tid etter hvert nylig avleirede lag. Metallet avkjøles til under 195°C.
- Under denne temperaturen skjer en transformasjon av krystallstrukturen i stålet", forklarer Eric Jägle, leder for gruppen "Alloys for Additive Manufacturing" ved Max-Planck-Institut für Eisenforschung og siden januar 2020 professor ved universitetet Bundeswehr München.
- Den såkalte martensittfasen dannes, og bare i denne fasen kan nikkel-titan-mikrostrukturene opprettes, melder Jägle.
For å tillate at det dannes utfellinger er det imidlertid nødvendig å varme opp igjen. For å oppnå denne oppvarmingen utnytter forskerne laserenergien som brukes til å avsette det påfølgende laget.
Denne tilleggseffekten forårsaket av laserstrålen til 3D-printeren blir referert til som indre varmebehandling. Lag som har blitt dekket direkte med neste lag uten avbrudd, forblir mykere fordi de ennå ikke er til stede som martensitt.
For første gang er forskerne i stand til å lage et komposittmaterial som består av lag med forskjellige egenskaper fra et enkelt utgangsmateriale direkte under produksjonsprosessen. Kürnsteiner er imponert over de mekaniske egenskapene til materialet som produseres på denne måten: - Testene bekrefter en utmerket kombinasjon av styrke og duktilitet.
Objekter med myk kjerne og hard overflate
Tallrike prosessparametere er egnet for å påvirke mikrostrukturene under 3D-printing. Jägle forklarer at i tillegg til, eller i stedet for pausetiden, som er variert i denne studien, kunne martensittdannelse og påfølgende utfellingsherding også kontrolleres ved å variere laserenergi, laserfokus eller utskriftshastighet samt eksterne oppvarmings- og kjøleteknikker.
I eksperimentene produserte forskerne kubeformede eller kuboidstålstykker med sidelengder på noen få centimeter som modeller for gjenstander med mer komplekse geometrier som er av interesse for datastyrt 3D-printing. De understreker også at Damaskus-lignende stål, med sine periodisk skiftende lag, bare er ett eksempel på lokal påvirkning av mikrostrukturen til en legering under produksjonsprosessen. For eksempel er det like mulig å lage verktøykomponenter med en kontinuerlig myk kjerne omgitt av et hardt, slitesterk ytre lag.
- Takket være vårt konsept med lokal kontroll ble dette oppnådd i ett enkelt produksjonstrinn - uten de ekstra prosesstrinnene som tidligere var nødvendige for overflateherding som nitrering, understreker Jägle. I følge forskerne kan det også være mulig å bruke teknologien til å lokalt justere andre egenskaper som korrosjonsbestandighet.
Full utnyttelse av potensialet
- Teknologien åpner nye dører for å justere lokale mikrostrukturer på en definert måte under additiv produksjon av til og med komplekse arbeidsstykker og gjør etterbearbeiding unødvendig, sier Kürnsteiner. Forskeren antyder også et paradigmeskifte:
- Inntil nå har det vært vanlig praksis å bruke konvensjonelle legeringer i 3D-printing. Imidlertid er mange kjente stål ikke optimalt egnet for additiv produksjon. Vår tilnærming er å utvikle nye legeringer som kan utnytte det fulle potensialet i 3D-printing.
For mer informasjon se: www.mpg.de
Kilde: Max-Planck-Institut für Eisenforschung GmbH