Stillhet betyr suksess
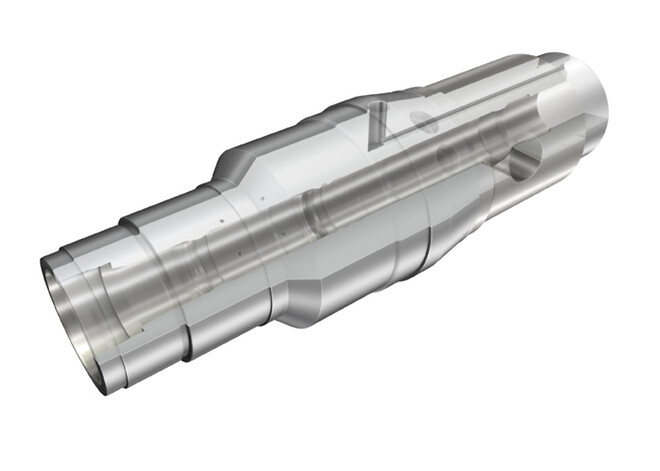
Men det skaper også potensial for endring til effektive og sikre prosesser. Dette potensialet har vært drivkraften bak utviklingen av vibrasjonsdempet maskinering, som i utgangspunktet var en løsning på et problem, men som i dag er en anerkjent måte å styrke produktiviteten på.
Stivhet mot vibrasjon
Forskning innen årsaker og mulige utbedringer av vibrasjonstendenser ble påbegynt allerede på 1960-tallet. Vibrasjoner hadde vært et problem innen maskinering så lenge metallskjæring har eksistert, og det var nødvendig å se nærmere på problemets natur der det oppsto, ved skjærekanten – spesielt med tanke på verktøyoverheng. Det ble fastslått at en vibrasjon kunne ses som et variabelt utslag i skjæreverktøyet, og ved intet eller minimalt utslag var det ingen vibrasjoner som påvirket maskineringen merkbart.
Vibrasjoner i skjæreverktøy utløses og opprettholdes av dynamiske skjærekrefter. Selv under kontinuerlig skjæring vil det være små, raske endringer i kreftene, som påvirker harmonien i skjæringen. De vanligste måtene å eliminere slike vibrasjoner på, er å øke den statiske stivheten i oppsettet, å redusere skjærekreftene som virker på verktøyet og å øke den dynamiske stivheten.
Naturlige vibrasjoner
Så snart man fant ut hvordan "klapring" i maskineringen kommer av vibrasjoner som oppstår i den dynamiske interaksjonen i skjæreprosessen, skjæreverktøyet, holdeverktøyet og maskinen, kunne man forske på enheter for passiv, dynamisk vibrasjonsabsorpsjon. Når det gjelder skjærekrefter som oppstår mellom verktøyet og arbeidsemnet, vil styrken i stor grad avhenge av skjærekantens kontaktgrad. Styrken belaster strukturen elastisk og fører til at verktøyet og arbeidsemnet forskyves, og dermed endres kontakten mellom verktøyet og arbeidsemnet: den udeformerte spontykkelsen. Eventuelle forstyrrelser i skjæreprosessen, for eksempel som følge av uregelmessigheter som harde punkter, forårsaker et utslag. Uansett hvor lite dette utslaget er, endrer det den udeformerte spontykkelsen, som fører til vibrasjoner ved variasjon av skjærekraften. Hvis den første vibrasjonen ikke håndteres, kan den være selvopprettholdende og bygge seg opp slik at maskinen svinger med naturlige vibrasjoner.
Reduseres til et trygt nivå
Den grunnleggende ideen for å motvirke vibrasjoner som oppstår i skjæreprosessen var å ha en masse opphengt i fjærer i en væske inne i verktøyskaftet. I begynnelsen var verktøyet som regel en borestang, men det ble senere konstatert at metoden kunne brukes for andre typer verktøy som var mottakelige for vibrasjoner. Den ekstra massen ble konstruert for å vibrere med en annen frekvens enn den som oppsto i skjæreprosessen, slik at den fikk en nøytraliserende (dempende) virkning. Vibrasjonstendenser ved maskinering kan naturligvis ikke fjernes helt, men de kan reduseres til et trygt nivå ved å sørge for riktig dempefunksjon i verktøyet.
Innebygde systemer
Da de nyskapende, dempede borestrengene av TNS-type ble introdusert på 1970-tallet, var det en revolusjon innen innvendig dreiing av dype hull. Stengene var tilgjengelige i tre diametere, konstruert for overheng på opptil ti ganger diameteren. Disse stengene hadde utskiftbare skjærehoder som kunne justeres radialt, og hadde mulighet for ulike holdertyper og vendeskjær. I tråd med den opprinnelige ideen inneholdt konstruksjonen en plugg av tung dempermasse, som var fjæropphengt i en spesiell type olje. Oljen absorberte energien fra eventuelle vibrasjoner under maskinering, og omdannet dem til varme som ble absorbert av oljen. Pluggens treghet, og dermed vibrasjonsfrekvensene som kunne håndteres, kunne stilles inn med en justeringsskrue på stangen. Denne innstillingen endret strammingen i opphenget, slik at man kunne oppnå optimal demping under bruk. Borestengene hadde også innebygde systemer for kjølemiddelsirkulasjon, for å bidra til å fjerne spon.
Et gjennombrudd
Dette medførte en dramatisk forbedring av datidens innvendige dreiing, som etter dagens standarder var relativt primitiv: Kapasiteten til å fjerne materiale kunne fordobles. Man kunne utføre maskinering som tidligere var umulig, og operasjoner som tidligere var flaskehalser ble mer effektive. Overflatefinishen ved et overheng på åtte ganger diameteren med høyere skjæredata ble redusert til Ra 1,3 mikron med den justerte stangen, sammenlignet med Ra 8,8 mikron med en konvensjonell, massiv borestang. Dette var et gjennombrudd innen finbearbeiding av hull.
Redusert nedetid
Med tiden ble det introdusert en kort, standard borestang – for bruk med overheng på opptil sju ganger diameteren – med den fordelen at det ikke var nødvendig å justere stangen for å optimere dempingen. Dette var en vesentlig forbedring i utviklingen av justerte borestenger, fordi vibrasjonsfrekvensene innenfor stangens bruksområde kunne dekkes i sin helhet med dempemekanismens konstruksjon. Det var en nyskapning som forenklet bruken av dempede verktøy og reduserte nedetiden for maskinene.
Viktig problemløser
Det neste trinnet var å utnytte verktøyets materialegenskaper ved bruk av sementert karbid. Det ble ikke bare brukt som det beste materialet til skjærekanten, men også til å øke verktøyets statiske stivhet. Sementert karbid har en gjennomsnittlig stivhet som er 2,5 ganger høyere enn stål, og ble tatt i bruk i form av hylser som ble festet rundt borestangen. På denne måten kunne overhenget til dempede borestenger økes til 12 ganger diameteren. Det innebar også at det ble rom for bruk av verktøy som roterende verktøy, og for å utnytte hele skjærepotensialet til vendeskjær i sementert karbid. Denne utviklingen førte til at dempede verktøy fikk en mye mer utbredt rolle som en viktig problemløser.
Egnet som spesialverktøy
Innen flere produksjonsindustrier har komponentene utviklet seg, og har medført et behov for maskinering av dype og noen ganger kompliserte borehull. Luftfarts-, energi- og presstøpingsindustrien er eksempler på områder der man finner svært krevende hull eller hulrom. Mange produsenter innen generell konstruksjon, bilindustri og maskinproduksjon har behov for å bruke dempede verktøy for å løse problemer. Det unike vibrasjonsdempende konseptet har vært tilgjengelig lenge som standardverktøy, men er også velegnet for spesialkonstruerte verktøy for spesifikke maskiner, komponenter og operasjoner. Eksempler på dette er sylindriske, avfasede, bøyde og elliptiske borestangseksjoner. Målet er å oppnå maksimal stivhet for å dempe vibrasjonene når det er behov for dyp verktøytilgang.
Forkorter leveringstiden
Veksten i olje- og gassindustrien innebærer at en rekke komponenter for dypboring må maskineres effektivt og sikkert, uten feilskjær. Plandreiebenker er stivere og bedre utstyrt for maskinering av de lange borestengene som kreves i deler for oljeleting, og har derfor hatt et langvarig oppsving. Det ble tidlig utviklet en rekke dedikerte dempede borestenger med diameter fra 80 til 300 mm, ideelle for grovbearbeiding og finbearbeiding når det er behov for stenger som håndterer ti ganger diameteren – og med spesialutgaver som tåler verktøyoverheng på 15 ganger diameteren. De første modellene ble justert manuelt med en radial justeringsskrue, og hadde utskiftbare skjærehoder. Eksempler på karbidforsterkede stenger som er laget for å håndtere de største diametrene veier nesten tre tonn. Disse stengene er en løsning for mange krevende operasjoner, og forkorter leveringstiden for deler som kreves på kort varsel i oljefeltene.
Velprøvd metode
For de fleste skrå CNC-dreiebenker, som er i utbredt bruk innen alle typer produksjon, ble det også tidlig utviklet en serie forhåndsjusterte, dempede stenger, vanligvis for diametere på 16 til 100 mm. Disse stengene er utstyrt med små, lette skjæreenheter, monteres med en kopling av serratert type, er lette å sette opp og raske og sikre å skifte ut. I begynnelsen fantes det en kort og en lang versjon av borestengene, for bruk med henholdsvis opptil sju og ti ganger diameteren. Disse verktøyene banet vei for en effektiv og enkel løsning på mange varierte innvendige dreieoperasjoner, og egnet seg for mange ulike bruksområder i ulike industrier. Denne serien kan regnes som forgjengeren til dagens SilentTools-verktøy, der sylindrisk fastklemming, Coromant Capto, CoroTurn SL og QC brukes til innvendig dreiing, sporfresing og gjenging. Rask utskifting av verktøy i dreiemaskiner er i økende grad blitt regnet som en viktig løsning for bedre maskineringsøkonomi, og dempede borestenger har vært en viktig del av dagens muligheter i maskineringssentre der rask utskifting av verktøyene er høyt prioritert ved maskinering. Forhåndsjusterte verktøy har gått fra å være bare en problemløser til å være en kvalifisert, velprøvd metode for å optimalisere driften.
Dype og komplekse fordypninger
Verktøy med mulighet for vibrasjonsdemping i ulike størrelser og lengder er også en viktig del av maskineringen i multimaskiner og fresemaskiner. I dag er det også utviklet dempeenheter for bruk med serraterte låseblader, konstruert spesielt for luftfarts- og energiindustrien for fremstilling av dype og komplekse fordypninger, ofte i krevende materialer.
Automatisk utskifting
Dagens utvalg av SilentTools-verktøy inneholder standardverktøy med diameter på opptil 250 mm. Den største borestangen som er levert hittil, har en diameter på 450 mm og er ment for overheng på ti ganger diameteren. Den veier sju tonn. Bruk av dempede verktøy øker også innen bruksområder med roterende verktøy og innen boreverktøy for maskineringssentre. I store maskiner, for eksempel ved bruk av ISO-standardiserte Coromant Capto C10-koplinger, er muligheten for rask utskifting en fordel når borestengene stikker så langt ut at det er vanskelig å utføre andre operasjoner med stangen i revolverhodet. I stedet for å sette opp den store borestangen hver gang, noe som i gjennomsnitt tar 40 minutter, tar hurtigutskiftingen bare fem minutter. Automatisk utskifting av verktøy er også installert for noen maskiner, for eksempel når en robot som også skifter komponenter typisk bytter ut en 100 mm borestang med maskineringsmulighet med et overheng på 14 ganger diameteren.
350 bar trykk
Når det gjelder eksempler på løsninger, ble bruken av store, dempede borestenger nylig videreutviklet sammen med en velkjent produsent av store fresemaskiner for innvendig dreiing av lange titan-titan-komponenter. De konstruerte stengene må ha en rekkevidde på 13 ganger diameteren – 176 mm med en rekkevidde uten oppstøtting på 2300 mm. De trenger også automatisk utskifting av verktøy foran på stangen. For å sikre enkel sponfjerning ble stangen i tillegg utstyrt med kjølemiddelforsyning med et ekstremt høyt trykk på 350 bar med moderne dyseteknologi for stråleassistert sponbryting ved skjærekanten. Dette bidrar til å sikre sponfjerning og riktig overflatefinish, samt bedre verktøylevetid og prosessikkerhet.
Planlagt løsning
Denne typen avansert vibrasjonsdempet maskinering med høytrykkskjøling har medført mer enn bare problemløsning. Den ble også en del av den planlagte løsningen, der den var avgjørende for å fremme produktiviteten samt prosessikkerheten for å unngå kassering av deler.
Du finner mer informasjon på www.sandvik.coromant.com